Metal check is a critical process in various industries, ensuring the integrity, safety, and quality of metal components. Whether you're in manufacturing, construction, or any other field that relies on metal materials, understanding how to effectively perform a metal check can save time, money, and even lives. In this article, we’ll explore the importance of metal checks, the methods used, and how they contribute to the overall quality of products and structures.
From detecting defects to ensuring compliance with industry standards, the process of metal checking is not just a technical necessity but also a strategic advantage. Industries such as aerospace, automotive, and construction rely heavily on the accuracy of metal checks to maintain safety and performance. With advancements in technology, the methods for conducting metal checks have evolved, offering more precise and efficient solutions.
In this guide, we will delve into the various techniques used in metal checking, including non-destructive testing (NDT), material analysis, and surface inspection. We'll also explore the tools and equipment commonly used in the process and discuss how to interpret the results. By the end of this article, you will have a thorough understanding of metal checks and their significance in maintaining high standards in industrial applications.
Read also:Matthew Husseys Wife Audrey Age And More Insights
Table of Contents
Introduction to Metal Check
Metal check refers to the process of inspecting and analyzing metal components to ensure they meet specific quality and safety standards. This process is essential in industries where metal components are subjected to high stress, pressure, or environmental conditions. The goal of a metal check is to identify any defects, inconsistencies, or weaknesses that could compromise the performance or safety of the material.
There are several reasons why metal checks are conducted. First, they help ensure compliance with industry regulations and standards, which are often stringent in sectors like aerospace and automotive. Second, they prevent costly failures or accidents that could result from undetected defects. Finally, metal checks contribute to the overall quality and reliability of products, enhancing customer satisfaction and trust.
Why Metal Check is Important
The importance of metal checks cannot be overstated, particularly in industries where safety and performance are paramount. Here are some key reasons why metal checks are crucial:
- Safety Assurance: Detecting defects early can prevent catastrophic failures, protecting both workers and the public.
- Cost Efficiency: Identifying issues during the manufacturing process reduces the need for costly repairs or replacements later.
- Regulatory Compliance: Many industries are subject to strict regulations, and metal checks ensure adherence to these standards.
- Quality Control: Metal checks help maintain consistent quality, which is vital for brand reputation and customer satisfaction.
In industries such as construction, where structural integrity is critical, metal checks are a non-negotiable part of the process. Similarly, in the automotive industry, metal checks ensure that components like engine parts and chassis meet safety and performance standards.
Common Methods of Metal Check
There are several methods used to perform metal checks, each suited to different types of materials and applications. Below are some of the most common techniques:
Non-Destructive Testing (NDT)
Non-destructive testing (NDT) is a group of analysis techniques used to evaluate the properties of a material without causing damage. Some of the most widely used NDT methods include:
Read also:Dynamic Duo Cristina Bernal Y Luis Coronels Impact In Entertainment
- Ultrasonic Testing: Uses high-frequency sound waves to detect internal flaws.
- Radiographic Testing: Employs X-rays or gamma rays to inspect the internal structure of metals.
- Magnetic Particle Testing: Detects surface and near-surface defects in ferromagnetic materials.
Material Analysis Techniques
Material analysis involves examining the chemical composition and physical properties of metals. Common techniques include:
- Spectroscopy: Analyzes the composition of metals using light or other electromagnetic radiation.
- Microscopy: Examines the microstructure of metals to identify defects or inconsistencies.
Surface Inspection Methods
Surface inspection focuses on identifying defects or irregularities on the outer layer of metal components. Techniques include:
- Visual Inspection: The simplest method, involving a visual examination of the surface.
- Dye Penetrant Testing: Uses a liquid dye to highlight surface cracks or defects.
Tools and Equipment for Metal Check
The tools and equipment used in metal checks vary depending on the method being employed. Below is a list of some commonly used tools:
- Ultrasonic Flaw Detectors: Used in ultrasonic testing to identify internal flaws.
- X-ray Machines: Essential for radiographic testing.
- Magnetic Yokes: Used in magnetic particle testing to create a magnetic field.
- Spectrometers: Analyze the chemical composition of metals.
- Microscopes: Used for detailed examination of metal microstructures.
Investing in high-quality tools and equipment is crucial for accurate and reliable metal checks. It's also important to ensure that operators are properly trained to use these tools effectively.
Interpreting Results
Interpreting the results of a metal check requires expertise and experience. The data collected during the inspection process must be analyzed carefully to determine whether the material meets the required standards. Here are some key considerations:
- Defect Identification: Determine the type, size, and location of any defects detected.
- Material Properties: Assess the chemical composition and physical properties of the metal.
- Compliance with Standards: Ensure the results align with industry regulations and specifications.
In some cases, additional testing may be required to confirm the findings or to gather more detailed information. It's important to document the results thoroughly and maintain accurate records for future reference.
Industry Standards and Compliance
Metal checks are often governed by industry standards and regulations, which vary depending on the sector. Some of the most widely recognized standards include:
- ISO Standards: International standards that provide guidelines for quality management and testing procedures.
- ASTM Standards: Developed by the American Society for Testing and Materials, these standards cover a wide range of materials and testing methods.
- ASME Standards: Focus on the design, construction, and inspection of pressure vessels and other industrial equipment.
Compliance with these standards is essential for ensuring the safety and reliability of metal components. Companies that fail to adhere to these regulations risk facing legal consequences, financial penalties, and damage to their reputation.
Conclusion and Next Steps
In conclusion, metal checks are a vital part of ensuring the quality, safety, and reliability of metal components across various industries. By employing advanced techniques such as non-destructive testing, material analysis, and surface inspection, companies can identify defects and inconsistencies early in the production process, preventing costly failures and ensuring compliance with industry standards.
As technology continues to evolve, the methods and tools used in metal checks will become even more sophisticated, offering greater precision and efficiency. To stay ahead, it's important for businesses to invest in training and equipment and to remain up-to-date with the latest industry standards and regulations.
We encourage you to share your thoughts or experiences with metal checks in the comments below. If you found this article helpful, please consider sharing it with others or exploring more of our content on quality assurance and industrial safety.
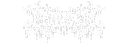
